|
(21), (22) Заявка: 2003136029/03, 15.12.2003
(24) Дата начала отсчета срока действия патента:
15.12.2003
(45) Опубликовано: 20.03.2005
(56) Список документов, цитированных в отчете о поиске:
Дерябин Ю.А. и др., Перспективы переработки Чинейских титаномагнетитов, Екатеринбург, Сред.-Урал. кн. изд-во, 1999, с. 160-161. RU 2087542 C1, 20.08.1997. RU 2206300 C2, 20.06.2003. US 4165234 A, 21.08.1979.
Адрес для переписки:
119017, Москва, Старомонетный пер., 31, ВИМС, патентная лаб.
|
(72) Автор(ы):
Тигунов Л.П. (RU), Кушпаренко Ю.С. (RU), Иванков С.И. (RU), Исаев С.В. (RU)
(73) Патентообладатель(и):
Всероссийский научно-исследовательский институт минерального сырья им. Н.М. Федоровского (ВИМС) (RU)
|
(54) СПОСОБ ОБОГАЩЕНИЯ КОМПЛЕКСНЫХ ЖЕЛЕЗОТИТАНВАНАДИЕВЫХ РУД
(57) Реферат:
Использование: изобретение относится к области обогащения полезных ископаемых и может быть использовано при получении железотитанванадиевых концентратов из комплексных одноименных руд для последующей металлургической переработки. Способ включает дробление исходной руды и последующую сухую магнитную сепарацию. Дробление проводят только с раскрытием совместных сростков титаномагнетитильменита от силикатных минералов при крупности от 50 мм до 15 мм, сухую магнитную сепарацию осуществляют при напряженности магнитного поля от 40 до 120 кА/м, удельной производительности от 50 до 100 т/час на 1 м ширины барабана магнитного сепаратора и влажности обогащаемой руды от 3 до 5%, с выделением в магнитную фракцию коллективного титаномагнетитильменитового концентрата для последующей плавки с получением ванадийсодержащего чугуна и высокотитановых шлаков для производства диоксида титана. 1 ил., 1 табл.
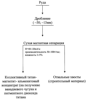
Изобретение относится к области обогащения полезных ископаемых и может быть использовано при получении железотитанванадиевых концентратов из комплексных одноименных руд для последующей металлургической переработки.
Известен способ обогащения комплексных железотитанванадиевых руд, включающий дробление и измельчение исходной руды до крупности – 0,5 мм, магнитную сепарацию с получением титаномагнетитового концентрата, гравитацию и электрическую сепарацию с получением ильменитового концентрата (Блинов В.А., Короленко Н.В. Минеральное сырье. Титан. Справочник – М.; ЗАО “Геоинформмарк”, 1998 – 49с, стр. – 32).
Недостатками известного способа являются значительная степень измельчения исходной руды (-0,5+0 мм), максимально удорожающая процесс, а также невысокое извлечение железа (75-76%) в титаномагнетитовый концентрат при больших потерях ванадия (до 40%) в хвостах обогащения. Эта технология сложна (включает дробление, измельчение, магнитную и электрическую сепарацию, гравитационное обогащение, сушку), энергоемка (измельчение и сушка), предусматривает применение малопроизводительного оборудования (гравитационное обогащение и сушка), требует больших расходов воды.
Наиболее близким по технической сущности и достигаемому результату к изобретению является способ обогащения комплексных железотитанванадиевых руд, включающий дробление исходной руды до крупности -12+0 мм и последующую сухую магнитную сепарацию (Дерябин Ю.А., Смирнов Л.А., Дерябин А.Л. “Перспективы переработки Чинейских титаномагнетитов”. Екатеринбург, Сред.-Урал, кн.изд., 1999, стр. 160-161).
К недостаткам известного способа следует отнести невысокое извлечение в железотитанванадиевый концентрат соответствующих металлов (80%; 71%; 84%), а также низкое качество концентрата (50% Fe, 9% TiO2, 0,85% V2O5), вследствие неэффективности режима сухой магнитной сепарации и относительного переизмельчения исходной руды.
Технической задачей изобретения является создание технологии обогащения комплексных железотитанванадиевых руд с высоким извлечением (85-90%) металлов в коллективный железотитанванадиевый концентрат при одновременном повышении его качества по железу, титану и ванадию.
Поставленная техническая задача решается таким образом, что в способе обогащения комплексных железотитанванадиевых руд, включающим дробление исходной руды и последующую сухую магнитную сепарацию, дробление проводят только с раскрытием совместных сростков титаномагнетитильменита от силикатных минералов при крупности руды от -50 мм до -15 мм, а сухую магнитную сепарацию осуществляют при напряженности магнитного поля от 40 до 120 кА/м, удельной производительности от 50 до 100 т в час на 1 м ширины барабана магнитного сепаратора и влажности обогащаемой руды от 3 до 5%, с выделением в магнитную фракцию товарного коллективного титаномагнетитильменитового концентрата для последующей плавки с получением ванадийсодержащего чугуна и высокотитанистых шлаков для производства диоксида титана.
Сущность заключается в следующем.
В результате проведенных исследований была установлена возможность выделения коллективного титаномагнетитильменитового концентрата для селективной плавки по технологии с получением богатого титаном шлака, пригодного для последующего производства пигментного диоксида титана. На основании установленной характерной особенности вещественного состава – достаточно тесной ассоциации рудных минералов и крупных размеров отдельно рудных и нерудных образований, было предложено проводить дробление без раскрытия совместных сростков титаномагнетитильменит, а с раскрытием срастаний рудных ассоциаций с силикатными минералами, при крупности дробления от –50 мм до –15 мм.
Исследования по сухой магнитной сепарации дробленной руды показали, что для осуществления поставленной цели – получения коллективного железотитанванадиевого концентрата, пригодного для плавки с получением ванадийсодержащего чугуна и высокотитановых шлаков – необходим строго определенный режим магнитной сепарации, крупнокускового материала. Экспериментально установлено, что оптимальными условиями процесса сухой магнитной сепарации исходного материала крупностью от -50 мм до -15 мм являются напряженность магнитного поля от 40 до 120 кА/м, удельная производительность сепаратора от 50 до 100 т в час на 1 м ширины барабана и влажность сепарируемого материала 3-5%. При таком режиме магнитной сепарации в сочетании с крупностью дробленой руды от -50 мм до -15 мм выделяется коллективный железотитанванадиевый концентрат с высокими технологическими показателями.
Изобретение позволяет в 3-5 раз снизить затраты на рудоподготовку, составляющие 60-80% общих затрат на получение кондиционных концентратов за счет отказа от операции измельчения, и реализовать сухой процесс обогащения (сухую магнитную сепарацию), исключив мокрую магнитную сепарацию, гравитационное обогащение, сушку и электрическую сепарацию, что существенно (на 40-60%) снижает расходы на собственно обогащение.
Пример конкретной реализации изобретения поясняется со ссылкой на графический материал, где на чертеже изображена схема и параметры процесса обогащения комплексных железотитанванадиевых руд.
Исследования проводились на пробе железотитанванадиевой руды с содержанием Fеобщ – 30%, ТiO2 – 10%, V2O5 – 0,56%.
Исходную руду подвергают дроблению сухим методом с раскрытием срастаний железотитанванадиевых минералов с силикатными минералами до крупности от -50 мм до -15 мм.
Дробленный минерал поступает на сухую магнитную сепарацию, которую осуществляют в следующем режиме:
влажность сепарируемого материала – 3-5%, напряженность магнитного поля сепаратора – 40-120 кА/м, удельная производительность на 1 м ширины барабана сепаратора – 50-100 т/час.
Разработанная технология обогащения комплексных железотитанванадиевых руд способствует эффективному отделению полезных минералов от силикатной породы и получения коллективного концентрата с содержанием Feобщ – 57-60%, TiO2 – 16-17%, V2O5 – 1-1,15% при их извлечении, соответственно,%, 95-97, 82-85, 96-98.
В таблице приведены данные, подтверждающие обоснованность предложенного технического решения – способа обогащения комплексных железо- титан- ванадиевых руд в сравнении с аналогом и прототипом.
Анализ полученных результатов показывает, что только при оптимальных условиях описываемого способа (опыты 3,4,5) достигается высокое извлечение ценных компонентов в коллективный железотитанванадиевый концентрат (95-98% Fe, 82-85% TiO2, 96-99% V2O5) при требуемом качестве по железу и титану 57-60% Fe и 17-18% TiO2.
При выходе за верхний и нижний пределы заявленных параметров процесса (опыты 6-9) снижается извлечение ценных компонентов в коллективный концентрат при одновременном ухудшении его качества по железу и титану.
Таким образом, использование изобретения решает проблему получения из комплексных железотитанванадиевых руд коллективного концентрата с высоким извлечением металлов (85-95%) для плавки по технологии с получением ванадийсодержащего чугуна и богатого титаном шлака, пригодного для производства диоксида титана.
Внедрение описываемого способа создает предпосылки для организации полного цикла обогащения “на борту карьера”, что снизит затраты на транспортировку и исключит необходимость строительства обогатительного предприятия в экологически более напряженном населенном пункте.
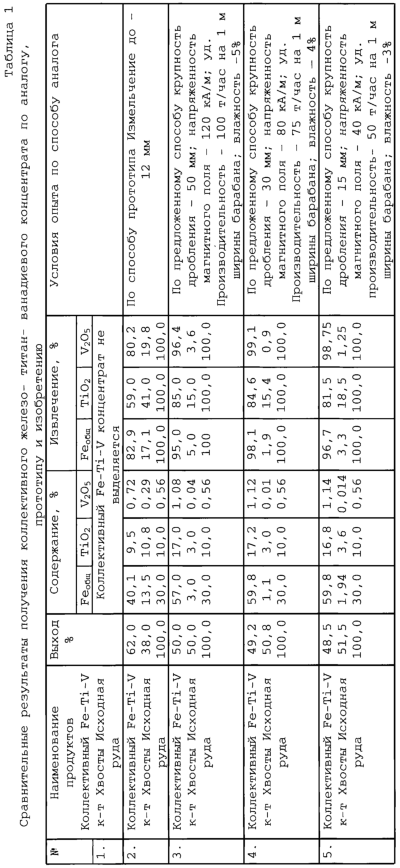
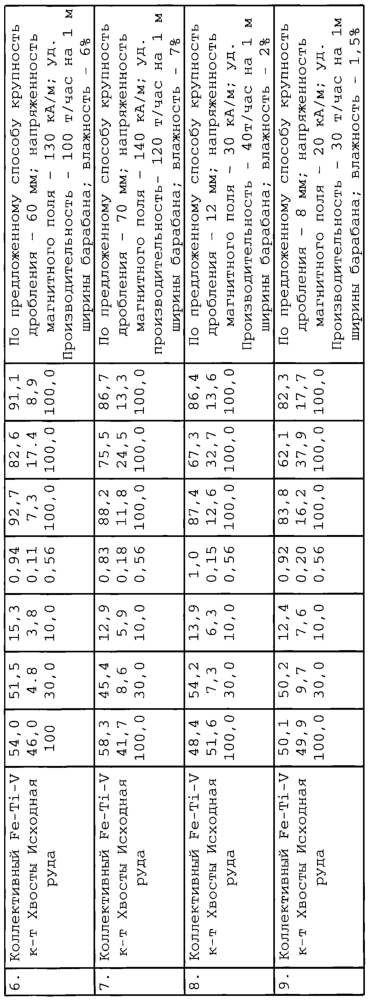
Формула изобретения
Способ обогащения комплексных железотитанванадиевых руд, включающий дробление исходной руды и последующую сухую магнитную сепарацию, отличающийся тем, что дробление проводят только с раскрытием совместных сростков титаномагнетита и ильменита от силикатных минералов при крупности от 50 до 15 мм, а сухую магнитную сепарацию осуществляют при напряженности магнитного поля от 40 до 120 кА/м, удельной производительности от 50 до 100 т/ч на 1 м ширины барабана магнитного сепаратора и влажности обогащаемой руды от 3 до 5%, с выделением в магнитную фракцию коллективного титаномагнетит-ильменитового концентрата для последующей плавки с получением ванадийсодержащего чугуна и высокотитановых шлаков для производства диоксида титана.
РИСУНКИ
MM4A – Досрочное прекращение действия патента СССР или патента Российской Федерации на изобретение из-за неуплаты в установленный срок пошлины за поддержание патента в силе
Дата прекращения действия патента: 16.12.2006
Извещение опубликовано: 20.02.2008 БИ: 05/2008
|
|