(21), (22) Заявка: 2003115919/02, 27.05.2003
(24) Дата начала отсчета срока действия патента:
27.05.2003
(45) Опубликовано: 10.01.2005
(56) Список документов, цитированных в отчете о поиске:
US 3895098 А, 15.07.1975. US 4376002 А, 08.03.1983. US 4604151 А, 05.08.1986. RU 2174437 С1, 10.10.2001. RU 2151759 С1, 27.06.2000. ЕР 0735013 А1, 26.05.1998.
Адрес для переписки:
607188, Нижегородская обл., г. Саров, пр-т Мира, 37, ФГУП “РФЯЦ-ВНИИЭФ”, начальнику ОПИНТИ В.Е. Миронову
|
(72) Автор(ы):
Леваков Е.В. (RU), Воронцов А.М. (RU), Горькаев Д.А. (RU)
(73) Патентообладатель(и):
Российская Федерация, от имени которой выступает государственный заказчик – Министерство Российской Федерации по атомной энергии, Федеральное государственное унитарное предприятие ” федеральный ядерный центр – Всероссийский научно-исследовательский институт экспериментальной физики” (RU)
|
(54) ПИРОТЕХНИЧЕСКИЙ СОСТАВ ДЛЯ ПОЛУЧЕНИЯ АЗОТА
(57) Реферат:
Изобретение относится к пиротехническим составам и может быть использовано для получения газообразного азота в источниках давления. Предложен пиротехнический состав для получения азота, содержащий азид натрия, оксид железа (III) и оксид титана (IV). Изобретение направлено на создание пиротехнического состава для получения азота, обладающего высокой надежностью горения, слабой зависимостью скорости горения от начальной температуры, стабильной скоростью газогенерации при повышенных давлениях с образованием твердых, нелетучих, пористых шлаков. 1 ил., 1 табл.
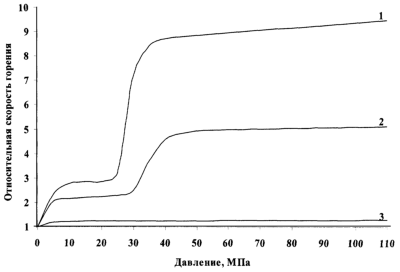
Изобретение относится к области пиротехники, в частности к пиротехническим составам, и может быть использовано для получения газообразного азота в источниках давления.
Большинство известных пиротехнических составов, генерирующих азот, в качестве носителя азота содержат азид натрия и предназначены для снаряжения генераторов газа, заполняющих подушки безопасности на автомобилях в аварийных ситуациях. В соответствии с этим заряд газогенератора должен выделять около 80 л холодного нетоксичного газа под давлением около 0,2 МПа за время 20-60 мс [1].
Однако имеется ряд технических задач, решение которых требует применения пиротехнического состава, способного обеспечить стабильно низкую скорость генерирования больших количеств газа в широком интервале давлений.
Известен пиротехнический состав, позволяющий реализовать стабильно низкую скорость генерации азота при давлениях до 110 МПа. Он содержит 63-80 мас.% азида натрия и 20-37 мас.% оксида вольфрама(VI) [2].
Приведенные авторами [2] результаты показывают, что, например, состав, содержащий 80 мас.% NaN3 и 20 мас.% WO3 горит со скоростью, линейно возрастающей от 6 мм/с до 9 мм/с в диапазоне давлений от 0,1 МПа до 110 МПа.
Сущность указанного технического решения заключается в снижении температуры горения и калорийности газогенерирующего состава за счет снижения доли окислителя и увеличения доли горючего по сравнению со стехиометрическим соотношением (стехиометрическое соотношение в данном случае 37/63 мас.% соответственно).
Это приводит к тому, что с окислителем реагирует лишь определенная доля горючего с образованием оксида натрия, свободного вольфрама и азота, при этом избыток азида натрия подвергается термическому разложению за счет тепла, выделяющегося при горении состава с образованием металлического натрия и азота.
Однако понижение температуры горения и калорийности состава крайне негативно сказывается на надежности его горения и обуславливает сильную зависимость скорости горения от начальной температуры [3].
Кроме того, наличие в продуктах горения легколетучих компонентов (свободного натрия и его оксида) требует применения мощной фильтрующей системы, а принимая во внимание их высокую химическую и коррозионную активность, значительно затрудняет утилизацию продуктов горения.
Известен пиротехнический состав для получения азота в результате реакции стехиометрического, или близкого к таковому, количества оксида титана(IV) с азидом натрия [4] (стехиометрическое соотношение в данном случае 23,5/76,5 мас.% соответственно).
Как предполагают авторы указанного изобретения, процесс горения этого состава может быть описан следующим уравнением:
4NaN3+ТiO2 2Na2O+Ti+6N2+6,4 ккал
Из приведенной схемы можно заключить, что состав имеет очень низкую калорийность и, как следствие, должен обладать низкой температурой горения и низкой надежностью горения.
Проведенные нами испытания указанного состава подтвердили это предположение.
Известен также состав для получения азота в результате реакции стехиометрического количества оксида железа(III) с азидом натрия [5] (стехиометрическое соотношение в данном случае 29/71 мас.% соответственно) по схеме:
6NaN3+Fe2O3 3Na2O+2Fe+9N2
Проведенные нами испытания указанного состава показали, что, несмотря на такие его достоинства, как высокое удельное газовыделение (360 см3/г), небольшой критический диаметр горения (~ 15 мм), генерирование практически чистого азота (>98 об.%), ему присущ и ряд существенных недостатков, в частности высокий процент несвязанного натрия в шлаках (до 20 мас.%), сильная зависимость скорости горения от начальной температуры и спонтанное увеличение (в 3-4 раза) скорости газогенерации при давлениях, превышающих 25-30 МПа (давление срыва).
Ввиду этого использование указанного состава невозможно в устройствах, требующих для своей стабильной работы монотонного увеличения давления до значений, превышающих 30 МПа.
Задачей, решаемой настоящим изобретением, является разработка пиротехнического состава для получения азота, обладающего высокой надежностью горения и стабильной скоростью газогенерации при повышенных давлениях с образованием твердых, нелетучих, пористых шлаков.
При использовании изобретения достигается следующий технический результат:
– высокая надежность горения (критический диаметр торцевого горения в стальном толстостенном стакане 7-8 мм);
– слабая зависимость скорости газогенерации от начальной температуры (температурный коэффициент скорости горения 4· 10-3 1/К);
– стабильная скорость горения состава в широком диапазоне давлений (увеличение давления с 0,1 МПа до 110 МПа приводит к увеличению скорости горения в 0,3 раза, для сравнения, в аналогичных условиях скорость горения прототипа увеличивается в 8-10 раз);
– при горении состава образуются твердые, нетекучие, химически малоактивные шлаки с высокой фильтрующей способностью (при горении состава-прототипа образуются полужидкие шлаки);
– генерируется чистый азот с пренебрежимо малым количеством примесных газов и пыли (содержание азота в образующемся газе более 99 об.%).
Для решения поставленной задачи в известный пиротехнический состав, содержащий азид натрия и оксид железа(III), согласно изобретению вводится оксид титана(IV) при следующем соотношении компонентов, мас.%:
азид натрия: 35-50;
оксид железа(III): 15-20;
оксид титана(1V): 30-50.
В данном случае, по сравнению с прототипом, введение оксида титана(IV) в указанных количествах позволяет полностью связать в волне горения легколетучие продукты горения (натрий и оксид натрия) в химически малоактивные титанаты, не плавящиеся при температуре горения состава, с выделением дополнительного количества тепла. Благодаря этому состав имеет достаточно высокую калорийность (1000-1500 Дж/г) и температуру горения (1500-1600 К), и, как следствие, низкий критический диаметр, высокую надежность торцевого горения и слабую зависимость скорости горения от начальной температуры.
Экспериментально установлено, что введение оксида титана(IV) позволяет значительно уменьшить поток тепла, переносимого из зоны горения в несгоревшую смесь легколетучими промежуточными продуктами горения состава.
Следствием этого является отсутствие наблюдаемого у прототипа резкого увеличения скорости горения.
Шлаки, после сгорания состава, представляют собой спекшийся пористый блок с геометрическими размерами исходного заряда, обладающий высокой фильтрующей способностью и малой усадкой.
На чертеже представлена зависимость относительной скорости горения (вычислялась как отношение скорости горения состава при давлении 0,1 МПа к скорости горения состава при заданном давлении) от давления для составов:
– кривая 1 – состав-прототип;
– кривая 2 – состав с рецептурой вне заявляемого диапазона соотношения компонентов;
– кривая 3 – заявляемый состав.
Для экспериментальной отработки заявленного состава были изготовлены образцы по следующей технологии.
1. Порошки входящих в состав компонентов после предварительной сушки и измельчения просеивали через сито с ячейкой 01 (100 мкм).
2. Взятые в необходимом количестве компоненты загружались в механический смеситель и перемешивались в течение 2 часов.
3. Образцы изготавливались методом прессования.
Сжигание образцов производилось в манометрической бомбе с регистрацией процесса горения с помощью датчика давления. Поджиг образцов осуществлялся электровоспламенителем с промежуточным безгазовым воспламенительным составом.
Разборка манометрической бомбы после испытаний показала отсутствие выноса продуктов горения в свободный объем, при этом шлаки представляли собой спекшийся пористый блок с геометрическими размерами исходного заряда. Это говорит об образовании твердых, нетекучих шлаков с высокой фильтрующей способностью.
Химический анализ шлаков показал отсутствие в них свободного натрия.
Анализ газа методом газовой хроматографии показал, что в нем содержится более 99 об.% азота.
Экспериментально определенные значения температуры горения (1500 – 1600 К), калорийности (1000-1500 Дж/г), критического диаметра торцевого горения (в стальном толстостенном стакане 7-8 мм) и температурного коэффициента скорости горения (4· 10-3 1/К) говорят о высокой надежности горения заявляемого состава и слабой зависимости скорости его горения от начальной температуры.
В таблице представлены характеристики заявляемого состава, состава-прототипа и состава с рецептурой вне заявляемого диапазона.
На чертеже представлены зависимости относительной скорости горения (вычислялась как отношение скорости горения состава при давлении 0,1 МПа к скорости горения состава при заданном давлении) от давления в системе для следующих составов:
– кривая 1 – состава-прототипа;
– кривая 2 – состава с рецептурой вне заявляемого диапазона соотношения компонентов (62 мас.% NaN3, 25 мас.% Fе2О3 и 13 мас.% TiO2);
– кривая 3 – заявляемого состава с рецептурой: 40 мас.% NaN3, 18 мас.% Fе2О3, 42 мас.% ТiO2.
Как следует из представленных данных, заявляемый состав (кривая 3) в отличие от прототипа (кривая 1) и состава с рецептурой вне заявляемого диапазона соотношения компонентов (кривая 2) способен обеспечить стабильную скорость генерирования газа (отсутствие давления срыва) в широком интервале давлений в системе (от 0,1 МПа до 110 МПа).
Характеристики пиротехнических составов для генерирования азота. |
Содержание компонентов, мас.% |
Скорость горения*, мм/с |
Давление срыва**, МПа |
Примечание |
NaN3 |
Fe2O3 |
TiO2 |
50 |
20 |
30 |
6,2 |
нет |
Заявляемый состав |
40 |
18 |
42 |
3,5 |
нет |
35 |
15 |
50 |
2,4 |
нет |
71 |
29 |
0 |
5,2 |
25-30 |
Состав-прототип |
62 |
25 |
13 |
7,4 |
35-40 |
Состав с рецептурой вне заявляемого диапазона соотношения компонентов |
* – при давлении 0,1 МПа и начальной температуре 295 К;
** – исследовалось до 110 МПа.
Литература
2. Патент РФ №2151759, МПК6 С 06 D 5/06, С 06 В 35/00, публ. 27.06.2000 г., бюл. №18. Газообразующий пиротехнический состав.
3. А.А.Шидловский. Основы пиротехники. М.: Машиностроение, 1973.
4. Заявка ФРГ №2327741, МПК6 С 06 D 5/06, публ. 20.11.75. Твердое средство для получения газа.
5. Патент США №3895098, МПК6 С 01 В 21/00, публ. 15.07.75. Способ и состав для генерирования азота (прототип).
Формула изобретения
Пиротехнический состав для получения азота, содержащий азид натрия и оксид железа (III), отличающийся тем, что он содержит оксид титана (IV) при следующем соотношении компонентов, мас.%:
Азид натрия 35-50
Оксид железа(III) 15-20
Оксид титана(IV) 30-50
РИСУНКИ
|